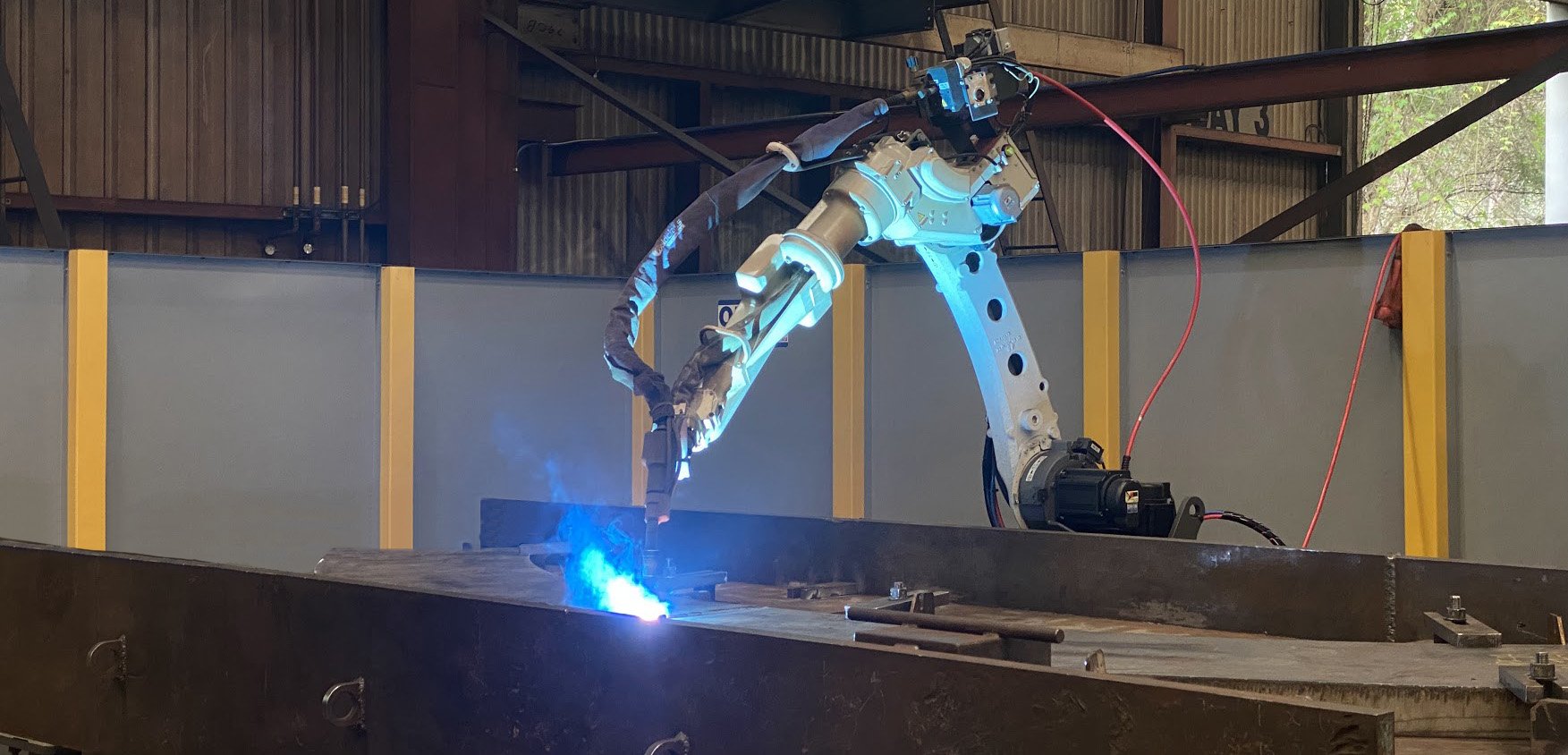
Large robotic welding cells
Standard solutions to tackling large, complex, and high-mix parts.
Powerful robotic welding systems engineered for performance. Orion’s large robot welding cells bring Panasonic’s 45+ years of welding robotics expertise to Australian and NZ manufacturers
Optimised cell access for easy operation and loading
Loading and unloading of large parts or jigs is simple with a large cell entrance, and a steel sliding door for side access for programming and maintenance.
Highly capable, fully integrated robots designed for welding.
Using Panasonic’s dedicated welding robot manipulators and integrated welding power source, and options for MIG or TIG, this system is flexible to suit your specific needs.
Harmonised movement options for large parts and part manipulation
By using Panasonic’s servo motor systems and integrated rotators, it’s possible to perform welds on large or complex parts where it’s a requirement for the part and/or robot to move whilst welding to maintain the ideal welding position.
Our international partnerships ensure tested, reliable and world-class solutions for large format robot welding systems
Orion’s direct partnership with world-leading integrator of Panasonic robots, Valk Welding, enables us to provide the Australian and New Zealand market with large-scale robot welding systems and advanced welding technology that not only outperforms the competition, but does so reliably using tried and tested, standardised technologies and mechanics engineered by Valk Welding.
Learn more about Valk Welding by clicking their logo below
Program your parts remotely using Panasonic’s DTPS offline programming software
Programming of large and complex parts can be done off-line, meaning the robot system can continue production while programming happens on a digital copy of the system on a computer.
This improves programming speed and robot arc-on time, as well as enabling your team to test production viability of parts on the robot system using CAD files before physical parts arrive.
World-class system calibration, combined with seam finding technologies like touch sensing, ensure that the programs made in DTPS can be sent straight into real-world production with confidence.
This option is essential for large systems to maximise your productivity, and enables the use of robotic welding even on high-mix, low volume production runs.
What’s included:
Panasonic TM or TL series robot arm with 1400mm, 1800mm, or 2000mm of reach
Panasonic’s G4 robot controller with integrated 350A or 500A power source
Servo-controlled wire feed system
Panasonic MIG or TIG torch
Panasonic’s dedicated welding programming teach pendant
Machined mild steel pedestal and master jig table with locator guides
Full steel guarding: RHS posts, sheet panels, and access door
Safety light curtains and controls designed to ISO and Australian Standards
Operator control stations for each work station
On-site installation
Jigging support
On-site training on Panasonic’s intuitive welding interface
Technical support from our experts with 35+ years’ experience
Direct supply of Panasonic consumables and spare parts through Orion
At Orion, we pride ourselves in providing standardised systems that cover a wide range of processes, materials and part sizes for your manufacturing needs.
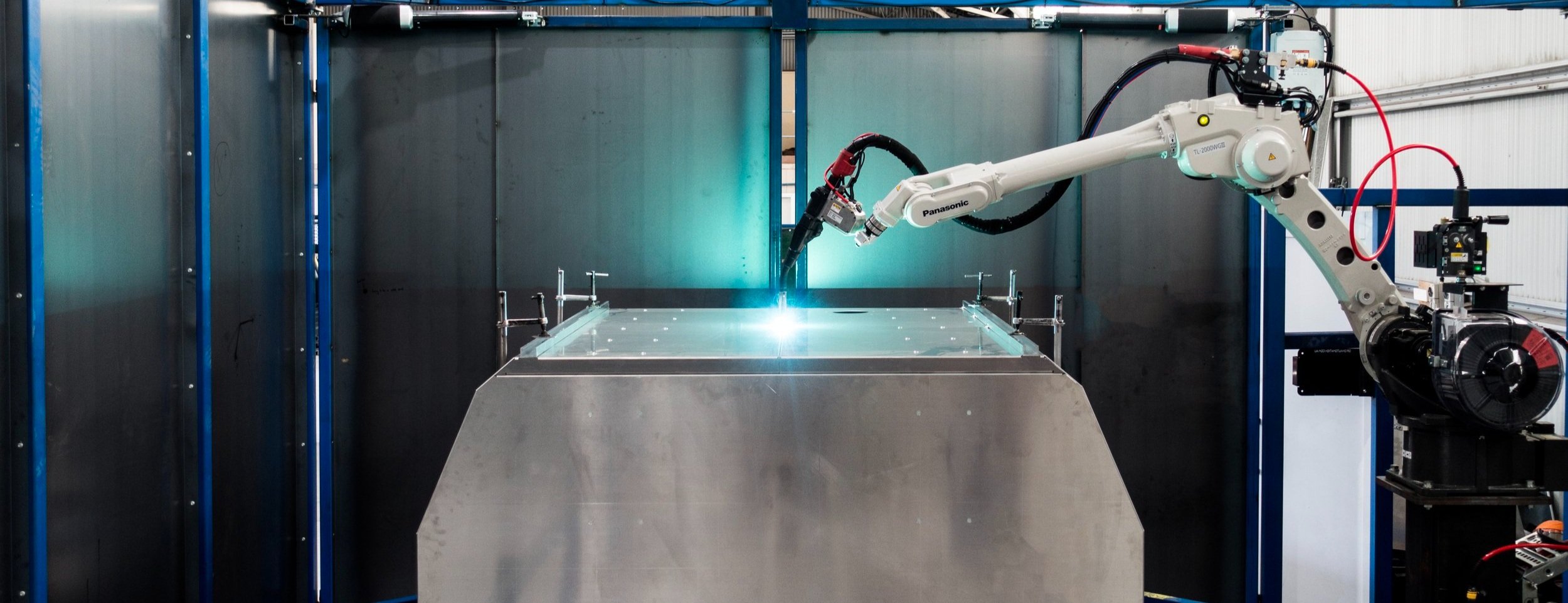
We are 100% focused on robot welding
Orion Automation Systems maximises your production using high performance industrial robotic welding systems, and the ongoing technical support to keep you in production for years to come.
Real Robots.
Real Experience.
Real Speed.
Real Productivity.
Options & Additions:
We are able to offer a wide range of options and technologies in addition to the base system, assisting in part manipulation, weld location tracking, and much more
These options include:
Single or Multi Axis Positioner Systems with payload capacity from 250 kg to 10,000 kg
Panasonic’s DTPS Off Line Programming Software
Part locating technologies such as touch sensing or laser seam tracking
Panasonic Process Control and production management software packages
On-torch fume extraction for MIG welding
Tool change systems