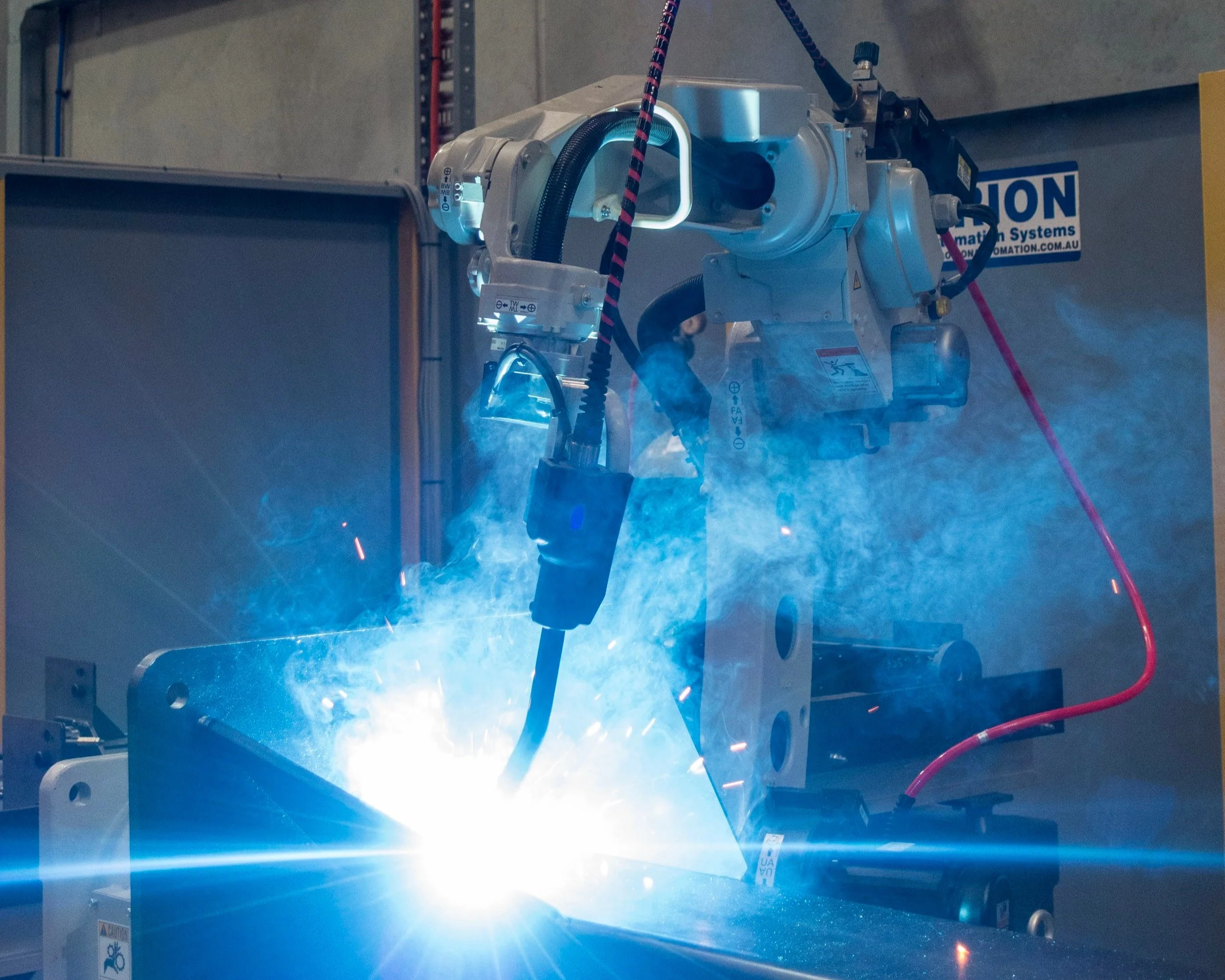
Technologies we offer
World-leading seam tracking, offline programming, or High-mix low-volume production.
Whatever your production challenge, it’s possible with the technologies Orion can integrate into our robotic welding systems
In-house CAD design
With our in house CAD technicians, we are able to produce innovative designs for our robotic welding cells, with every aspect designed specifically to suit the welding environment. Solid steel guarding is both secure and protects your shop staff from the welding arc, modular jig tables can make your production more versatile, and more.
This also allows our cell designs to be highly customisable, whilst still utilising our standardised designs. Because of this, Orion is able to work alongside you and tailor our range of standard cells to suit your needs, pulling from our experience to ensure that your cell suits your product and workshop straight away.
Panasonic DTPS offline programming software
Programming of large and complex parts can be done off-line, meaning the robot system can continue production while programming happens on a digital copy of the system on a computer.
This improves programming speed and robot arc-on time, as well as enabling your team to test production viability of parts on the robot system using CAD files before physical parts arrive.
World-class system calibration, combined with seam finding technologies like touch sensing, ensure that the programs made in DTPS can be sent straight into real-world production with confidence.
This option is essential for large systems to maximise your productivity, and enables the use of robotic welding even on high-mix, low volume production runs
Seam Tracking
Touch Sensing
Touch sensing enables the robot to physically touch the part before welding to determine how much the seam location varies from what has been programmed, and automatically adjust the weld point to account for this.
Touch sensing is perfect for parts that do not warp while welding very much, and for locating most hand-tacked parts
Circular pattern laser seam tracking using the ARC-EYE camera by Valk Welding
Valk Welding’s unique ARC-EYE camera technology employs the use of a circular pattern, servo-driven laser camera installed close to the welding torch’s nozzle. Specifically designed for Panasonic robot welding systems, the ARC-EYE camera can be used to provide real-time weld seam tracking, even on reflective parts like Aluminium checker plate that are nearly impossible to track with traditional line pattern lasers.
ARC-EYE cameras are the ideal solution for welding large parts that deform during welding, and for welding of complex and hand formed assemblies.
The above system was installed by Orion Automation Systems in Australia, and utilises both touch sensing and ARC-EYE seam tracking to perform full length welds on aluminium fishing boat hulls for a renowned Australian boat brand.
Touch sensing is used to find the rough location of components around the hull, with the ARC-EYE camera then doing the heavy lifting to maintain the correct welding path on welds up to 8 metres long.
With these technologies, it’s possible to automate parts that would previously be unthinkable to weld with a robot.
Valk Welding torches with on-torch fume extraction
Our partnership with world-leading integrator of Panasonic robots, Valk Welding, enables us to integrate their advanced welding torches, with the option of on-torch fume extraction to help your workshop meet the new standards surrounding air cleanliness in fabrication workshops.
Valk Welding design and build their own welding torches in the Netherlands to use on their own systems, and offer a host of unique features including an interchangeable torch neck, pneumatic shock sensor, and highly flexible power conduit.
Learn more about Valk Welding’s MIG II torch by clicking their logo below:
Part positioning and harmonised manipulation
Utilising Panasonic’s range of servo driven positioners, as well as standard solutions from Valk Welding which utilise Panasonic servo motors, harmonised motion can be used to weld large and complex parts whilst maintaining the proper weld attitude and reducing stop/starts on long welds.
Harmonised motion works by precise calibration between the robot and the rotator or linear track, meaning the operator simply moves the part and the robot where they’d like it to weld, and the robot will ensure that the weld speed is kept consistent.
This feature is critical on many circular parts, such as pipe spools with large branch intersections, or longer parts where the robot is required to travel down a track to continue its weld.
Orion Automation is able to provide standard solutions for even multi-axis integrated rotators up to 10,000kg capacity, ensuring that your part positioning needs are covered.
Thick plate welding solutions
Panasonic’s robots are purpose-built to withstand heavy welding
With up to 500A high duty cycle integrated power sources, and water cooled torches rated for it, you can trust that the equipment we supply is up to the task of the heavy duty welding you require. Panasonic’s robot manipulators are designed specifically for the tough environment of a welding workshop with an all-metal build, integrated servo-driven wire feeder and protected internal cable harnesses (including all welding power, sensors, and electrical cables).
Automated multi-pass welding
Previously, a 20 pass weld meant 20x the programming, now it’s just as simple as any other weld.
Using Panasonic’s optional Thick Plate software, it’s possible to automate detailed, multi-pass welds on heavy material. Once the operator teaches the root run, they are able to simply input the offset and weld conditions for the following runs, and the robot will automatically shift the weld path based off of the information the operator provided.
Adaptive multi-pass welding using ARC-EYE cameras
Using the ARC-EYE circular laser seam tracking camera, it’s possible for the robot system to analyse a weld prep, and automatically decide on the best path for filling it. This world-leading technology enables the use of robotic welding on mission-critical heavy fabrication, and heavy fabrication with inconsistent weld preps.
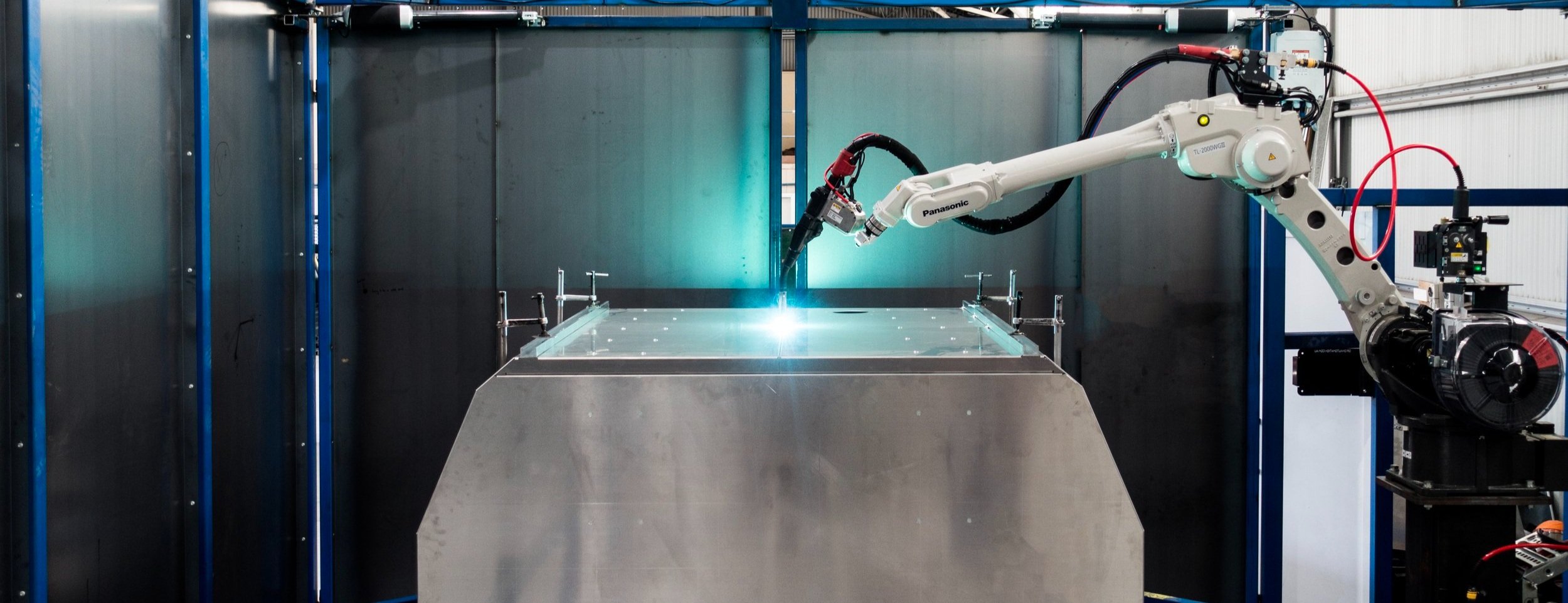
We are 100% focused on robot welding
Orion Automation Systems maximises your production using high performance industrial robotic welding systems, and the ongoing technical support to keep you in production for years to come.
Real Robots.
Real Experience.
Real Speed.
Real Productivity.

Contact Us:
Contact us at any time by phone, email or the form in this section.
Jeff Fordham - Managing Director
Mobile: 0450 546 835
International: +61 450 546 835
Email: Jeff@orionautomation.com.au